Case Studies: Use Green Engineering in the Design and Operation of Industrial Processes
Green engineering is being incorporated across the chemical processing industry to lower risk, reduce waste, and improve the economics of chemical manufacturing. Toward that effort, EPA’s Green Engineering Program provides case studies that can be used as examples in the application of the green engineering principles to industrial processes.
These case studies are meant to be:
- Stepping stones for those with interests in the chemical processing industry to use in developing their own industry-specific scenarios.
- A way to improve across government and non-government entities the knowledge and broad application of the nine Principles of Green Engineering.
Read the Principles of Green Engineering.
Case studies: Green engineering in industrial processes
Reactive distillation
Professors M. Doherty and M. Malone of the University of Massachusetts Department of Chemical Engineering explored the topic "Recent Advances in Reactive Distillation." In comparing traditional versus reactive distillation methods, such as in the production of methyl acetate, the latter methods have the advantage of being able to:
- Improve selectivity
- Reduce raw materials usage
- Reduce byproducts prevent pollution
- Reduce energy use
- Handle difficult separations
- Avoid separating reactants
- Eliminate/reduce solvents
- Enhance overall rates
- "Beat" low equilibrium constants
Example: Graphic comparison of production of methyl acetate using traditional and reactive distillation methods.
Reducing automobile emissions and saving energy
William Obenchain and Marcel van Schaik of the American Iron and Steel Institute, and Pete Peterson of the U.S. Steel Group conducted a case study on the UltraLight Steel Auto Body-Advanced Vehicle Concepts (ULSAB-AVC), in which reductions in automobile emissions and improvements in gas mileage were observed as a result of using lightweight steel in the construction of cars.
The ULSAB-AVC is a complete conceptual design for steel intensive compact and mid-size sedans. The designs were developed by a consortium of 33 steelmakers from around the world. The designs specify gasoline and diesel powered models; in the U. S. combined driving cycle the mid-sized sedan will achieve 52 miles per gallon when powered with a gasoline engine and 68 miles per gallon if equipped with a diesel engine. This equates to only 0.32 (diesel) - 0.38 (gasoline) lbs of CO2 per mile.
ULSAB-AVC: Comparison of mileage and CO2 emissions
U.S. C.A.F.E. standard | ULSAB-AVC Gasoline | ULSAB-ABC Diesel | |
---|---|---|---|
U.S. combined [mpg] | 27.5 | 52 | 68 |
CO2 emission [g/km] | 204 | 108 | 92 |
CAFE = Corporate Average Fuel Economy Standards for automobiles and trucks
Minimizing hazardous chemicals in the paper industry
Carl Houtman of the U.S. Department of Agriculture (USDA) Forest Product Service and of the University of Wisconsin at Madison conducted a case study on minimizing the use of hazardous chemicals in the paper industry. To eliminate the use of and exposure to hazardous chemicals in the bleaching process, a new delignification agent (a polyoxometalate, or POM) is used to provide the basis for closed-mill bleaching technology.
This technology eliminates the use of a hazardous chemical while maintaining effective lignin removal. The two flow charts below compare the traditional bleach process and the new "green" process using POM.
Graphic comparison of lignin removal from wood using traditional and "green" methods.
While this delignification process completely eliminates beach plant effluent, it requires increased steam and energy usage as well as new capital equipment. As demonstrated in the table below, the trade-offs are that the POM process requires higher process flow temperature and has a high steam requirement to run the oxidative reactor.
Furthermore, the increased capital cost in mills already built prohibits immediate implementation. The challenge will be to reduce process temperature and to eliminate the oxidative reactor to decrease steam requirements.
Paper bleaching: comparison of process stream and energy inputs
Process Stream Inputs | Energy Inputs | |||||||
---|---|---|---|---|---|---|---|---|
NaOH | O2 | H2SO4 | CIO2 | H2O2 | POM | Electricity (kW-hr/MT) |
Steam (kg/MT) |
|
POM | 137 | 0.27 | 277 | 2,858 | ||||
DEop | 24 | 5 | 5 | 18.3 | 6 | 281 | 1,693 |
POM = polyoxometalate process, uses no ClO2 or NaOH, DEop = traditional method of bleaching
Minimizing worker exposure to mist in the auto industry
Exposure to mist from machining fluids can cause serious health problems, including cancer, respiratory problems, and allergic reactions. To limit exposure from inhalation of this mist, Professors Manke, Gulari, and Smolinski of the Wayne State University Department of Chemical Engineering and Materials Science tested the effect of adding polymers to both water-based and straight-oil machining fluids.
A cost-effective method of reducing mist from oil-based fluids has already been widely implemented in the auto industry. For water-based fluids, however, the economics of mist suppression techniques are not yet as favorable, and engineers continue to look for practical ways to meet this challenge.
For straight oil fluids, polyisobutylene (PIB) can be added to control mist. An addition of 70 ppm of PIB results in a 40 percent reduction in average mist levels and a 67 percent reduction in peak mist levels. This additive has been used extensively in auto manufacturing facilities. Its costs are relatively low and only weekly replacement is required.
Graphic showing influence of polymers on atomization of machine fluids.
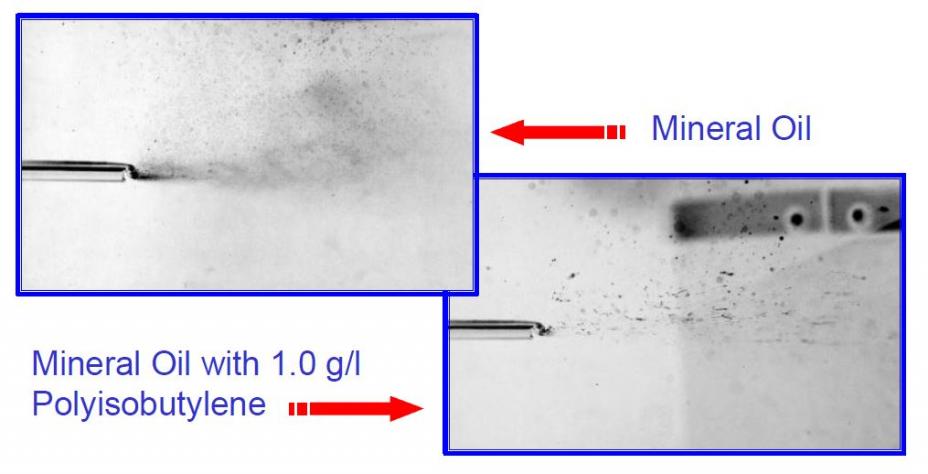
Chart showing reduction of mist of machining fluids using PIB additive.
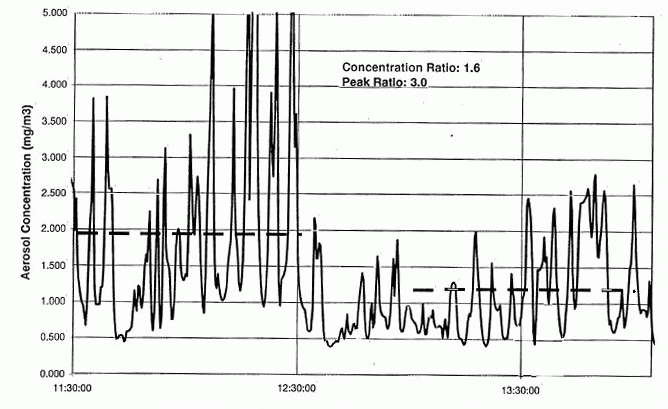
- 40% reduction in average mist levels
- 67% reduction in peek mist levels
- 24 hours plus service life
To control mist from water-based machining fluids, engineers are exploring the use of polyethylene oxide (PEO) for this purpose. The results are promising. However, high treatment levels are needed (up to 500 pm), the polymer is relatively costly, and daily replacement is required.
To improve the economics of treatment for water-based fluids, researchers are investigating optimization of polymer-surface interactions and synthesis of "designer" antimisting systems.