RHC for Industrial Processes
- About this sector
- Sector opportunities and challenges for project development
- Costs of RHC technologies
About This Sector
In 2013, the total delivered energy consumption of the United States industrial sector was estimated to be nearly 24 quadrillion Btu.1 Industrial process heating alone accounts for more than 5 quadrillion Btu of energy consumption.2 Industrial process heating is part of materials industries as well as the manufacturing of value-added products, and it can represent anywhere from 2 to 15 percent of the total cost of products.
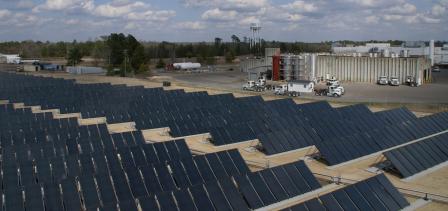
Credit: FLS Energy
The highly diverse nature of industrial process heating applications can present significant challenges. Several international studies indicate that as much as:
- 30 percent of industrial heating needs require heat below 212°F;
- 27 percent can be met with heat between 212 and 750°F; and
- 43 percent require heat above 750°F.3
Many commercially available renewable heating and cooling technologies can supply heat at these useful levels to address industrial process heating needs.
Sector Opportunities and Challenges for Project Development
Several factors make industrial process heating a good candidate for renewable heating and cooling (RHC) projects:
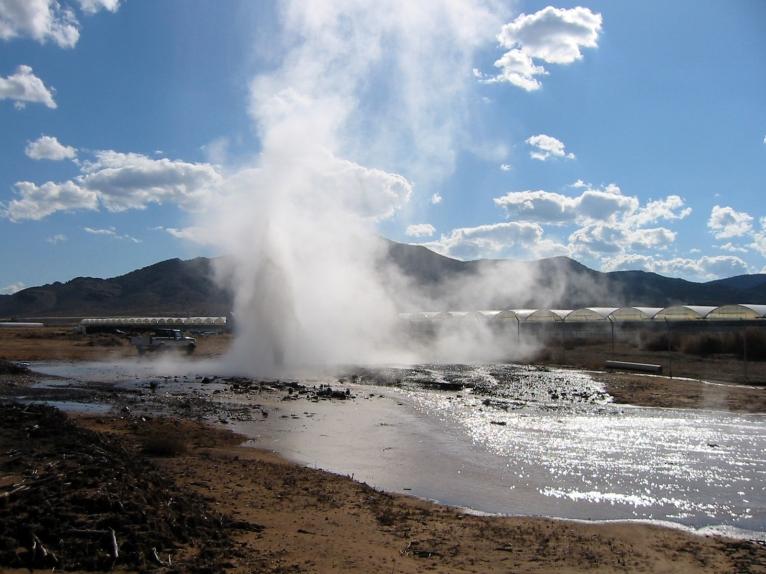
Credit: Robert Blackett, NREL
- Nearly 60 percent of industrial heating needs can be met with currently available low- or medium-temperature renewable heating technologies.
- Renewable heating technologies can serve as an effective “pre-heat” complement to conventional fuel sources in meeting industrial heating needs.
- Renewable heating and cooling resources can provide an economic hedge against volatile fuel prices. Approximately 44 percent of industrial primary energy (energy consumed onsite, excluding electricity generated offsite) comes from natural gas, and approximately 40 percent comes from petroleum, two of the more price-volatile energy sources available.4
- In addition to serving low- and medium-temperature process heat, renewable heating and cooling technologies can be particularly useful for heating or cooling industrial buildings with the use of under-floor heating systems.
Renewable heating and cooling projects in this sector also face some challenges:
- Many industrial facility managers are unaware of available renewable heating technology options.
- In some applications, renewable heating projects might only “scratch the surface” of a facility’s total heating energy use. Facility managers might need to be convinced that renewable heating projects are worth the effort given the systems’ relatively small impact.
- The integration of solar heat into industrial processes is more complex than the design of common heat supply technologies. Variable energy sources present unique challenges for process integration because the supply of energy is non-continuous. System design must account for the standstill behavior of the renewable heating plant, as it is possible that the heat produced might not be used on weekends or holidays, leading to overheating concerns for the system.
- Although thermal energy storage is generally not required when renewable heating and cooling serve as a “pre-heat,” in some applications storage can be desirable. Storage can drastically increase the overall cost of a renewable heating system or be difficult to site within existing building infrastructure.
Costs of RHC Technologies
The total cost of developing renewable heating and cooling systems can vary based on a number of factors, including the state policy environment, physical geography, available incentives, labor rates, and more. The following cost information is sourced from the National Renewable Energy Laboratory (NREL)5 and should not be interpreted as statistically accurate or sector-specific, but instead should be taken only as rule-of-thumb information and used only for a first-pass screen of economic viability. Visit NREL's website for more detailed information about other costs and typical project lifetimes.
Technology type | Mean installed cost ($ per square foot) |
Installed cost range (+/- $ per square foot) |
Operation and maintenance cost |
---|---|---|---|
Solar water heating: flat-plate and evacuated tube collectors |
$141 | $82 | 0.5 to 1.0% of initial installed cost |
Solar water heating: plastic polymer collector (unglazed) |
$59 | $15 | 0.5 to 1.0% |
Technology type | Mean installed cost ($ per ton) |
Installed cost range (+/- $ per ton) |
Operation and maintenance cost |
---|---|---|---|
Ground source heat pump | $7,518 | $4,164 | $109 +/- $94 |
Technology type | Mean installed cost* ($ per kilowatt) |
Installed cost range (+/- $ per kilowatt) |
Fixed operation and maintenance cost ($ per kilowatt) |
---|---|---|---|
Biomass wood heat* | $600 | $361 | $91 +/- $33 |
*Biomass wood heat converted from thermal energy capacity (Btu per hour)
- Learn more about solar, geothermal, and biomass technologies.
- Learn more about industrial process heat.
- Learn more about financial incentives for RHC.
1 U.S. Energy Information Administration. 2014. Annual Energy Outlook 2014.
2 CSGI, Inc., and Energetics, Inc. 2001. Roadmap for Process Heating Technology (54 pp, 577K, About PDF).
3 International Energy Agency, Solar Heating and Cooling Program. 2008. Potential for Solar Heat in Industrial Processes Exit.
4 U.S. Department of Energy, Energy Information Administration. 2014. Annual Energy Outlook 2014: Energy Consumption by Sector and Source. These percentages are for 2013.
5 National Renewable Energy Laboratory. 2013. Distributed Generation Renewable Energy Estimate of Costs. Updated August 2013.